
Development of “Robot Arm / Access Rail”; Testing of device for access inside the pedestal [Developed by Mitsubishi Heavy Industries (MHI)] (March, 2017)
Mar.21,2017
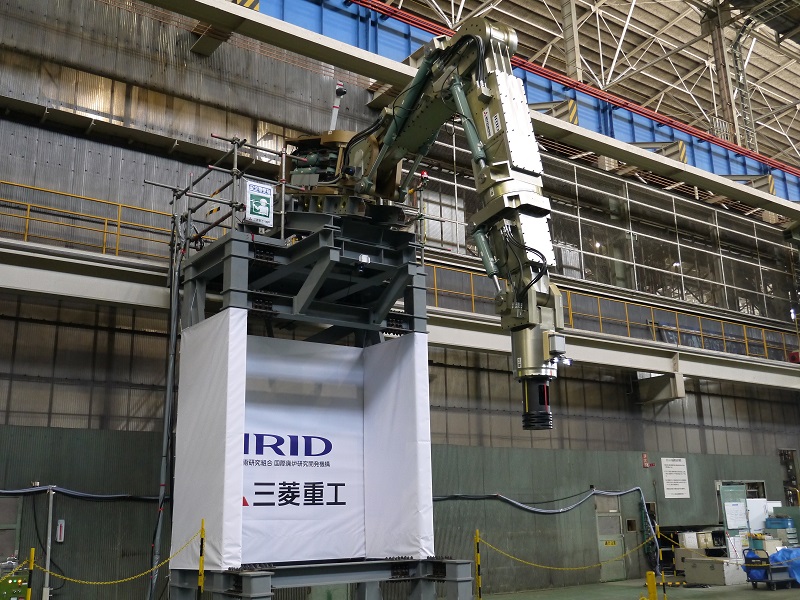
As part of its R&D efforts for decommissioning of Fukushima Daiichi Nuclear Power Station (NPS), IRID is involved in the Project for Development of Fundamental Technologies for Retrieval of Fuel Debris and Internal Structures; the Subsidy Project of Decommissioning and Contaminated Water Management,.
Here, we introduce “R&D updates of access devices inside the pedestal” which is a key access technology for Partial Submersion Side Entry Method, as one of the fuel debris retrieval methods.
(1) R&D on Access Rail
[Access rail function]
・Guidance into the pedestal by robot arm for fuel debris retrieval (guidance up to center of pedestal is assumed)
・Transportation of fuel debris storage unit canister between a work cell and inside the pedestal
(2) R&D on Robot Arm
[Robot arm specification]
・Loading at the tip: 2,000kg ( a diameter of 60 mm of core boring is assumed)
・Arm length: 7,100mm (the access route is assumed to be from the bottom of RPV to approximately 1.5m below the bottom of pedestal)
・Accuracy of high positioning with multiple axes (six aces)
[Attachment: “Overview of Access Rail and Robot Arm]
https://irid.or.jp/wp-content/uploads/2017/03/20170321.pdf
<Video image> * Link to the YouTube site.
![]() |
![]() |
32 X speed Access Rail (side view) | 32X speed Access Rail (front view) |
![]() |
|
Robot Arm (edited version) |
<Reference>
[Access Rail]
![]() |
![]() |
![]() |
![]() |
![]() |
[Robot Arm]
![]() |
![]() |
![]() |
![]() |
![]() |
Inquiries regarding this topic may be directed to IRID viaE-mail