
Completion of Preparation for Full-Scale Test Facility Simulating the Lower Part of the PCV and Future Test Plans (October 13, 2016)
Oct.13,2016
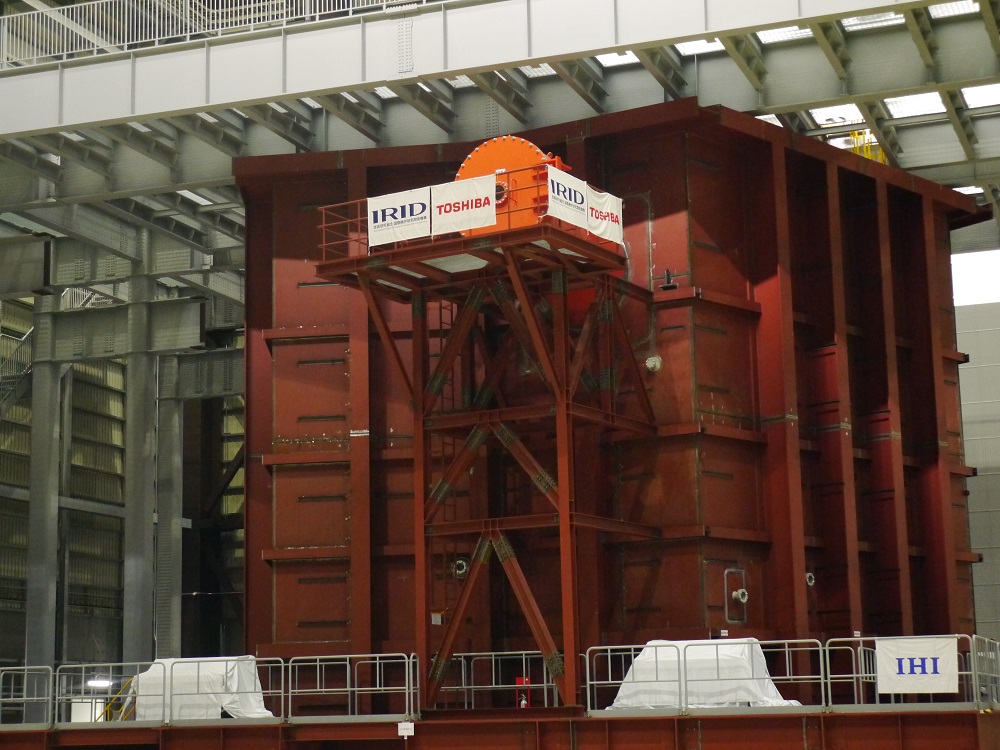
A full-scale mock-up facility* is now ready for testing purposes to establish technology for repairing water leakage points in the lower part of the Primary Containment Vessel (PCV).
* This test facility simulates vent pipes, the suppression chamber (S/C), and torus room wall found in the lower part of the PCV in Fukushima Daiichi Nuclear Power Station (NPS) Unit 2. The facility is of full-scale size, but represents a 1/8 portion of the circular S/C.
Between FY2014 and FY2015, IRID conducted a series of elemental tests (including tests of technology for strengthening S/C support columns and for the development of water stoppage methods, such as injection of material into vent pipes and filling of the S/C) in order to develop technology to repair / stop water leakage in the lower part of the PCV.
In addition to full-scale combined testing based on elemental test results obtained to now, IRID plans to use this test facility to collect knowledge and expertise in the development of technology to repair the lower part of the PCV, including confirming remotely operated procedure for on-site work. (Research period: FY 2016 – FY2017, two years in total)
[Future Developments]
The workability verification test for strengthening S/C support columns (using water as simulated reinforcement material) will start between November and December 2016. A series of full-scale tests for development of construction methods is planned for completion by the next summer of FY2017. We expect to publish updates accordingly when the test schedule is confirmed.
![]() |
![]() |
(Figure 1) Image of testing device | (Figure 2) size of testing device |
![]() |
![]() |
Full view of full-scale mock-up S/C | Structure building (Height: approx. 15m, Width: approx.19m) |
![]() |
![]() |
Measuring oxygen inside a shell before entering the facility | Shell measurement record |
![]() |
![]() |
Access port from operation floor to the mock-up facility | Access port to inside S/C |
![]() |
![]() |
Entering S/C | Upper part of S/C (External side torus room wall) |
![]() |
![]() |
Upper part of S/C and vent pipes (Torus wall is behind) | Inside S/C (Down-comer ring header and down-comer) |
![]() |
![]() |
Inside S/C (Down-comer ring header) | Inside S/C and tip of a vent pipe (No simulated vacuum breaker) |
[Manufacturing process of full-scale testing device]
![]() |
![]() |
Installed S/C support columns (Taken image on December 8, 2015) | Installed S/C (Taken image on December 23, 2015) |
![]() |
![]() |
Installed wall surface of torus room (Taken image on February 9, 2016) | Installed a vent pipe (Taken image on February 15, 2016) |
Click here to see manufacturing process of testing device in detail.
[Reference]
・IRID Annual Research Report 2015
Development of repair and water leakage stoppage technology for leakage points inside the PCV
Full-scale test for repair and water leakage stoppage technology for leakage points inside the PCV
Inquiries regarding this topic may be directed to IRID via E-mail